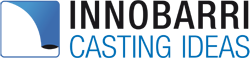
Due to the highly exigent environment and the needs of research and development in which Fumbarri’s activities take place and known the compromise with them that the entire Fumbarri team shares, Fumbarri has decided to create an R+D Unit; Innobarri.
The privilege position at the market that Fumbarri has, being a meeting point for customers, research centers, providers and laboratories, which allows us to analyze and resolve innovative challenges together with our partners, offering effective solutions today, to concrete iron heavy casting sector problems.
Fumbarri has equiped Innobarri with state of the art technologies, combining it with our more than 60 year experience. Furthermore, Fumbarri has interiorized Innovation, providing Innobarri with each and every equipment and technician part of Fumbarri, becoming the biggest laboratory that we could desire.
"Let us face, innovating today, tomorrow challenges"
Fumbarri’s Team
Research + Development + Innovation
Among the years Fumbarri has become a Strategic Partner for several research centres, laboratories and engineering for its wide range of possibilities to test new materials, processes and products, as well as for our open mind and innovative culture facing new challenges.
Therefore has reinforced its investigation activities and its technological and innovative development, fulfilling the highest efficiency levels, while searching the solutions to the challenges proposed, putting innovation as a critical key to success.
R+D Proyects
- Design new prototyping system for the wind energy sector by applying the process lost casting model. CDTI - Innovation Projects and Development - CDTI - Individual Projects Research and Development (SMEs)
- Design and development of a system for applying paint refractory polystyrene models in model casting lost.
- OPCOL: Optimization of the manufacturing process of a new copolymer for casting parts in the lost model aimed at the machine tool sector. GAITEK 2015
- SILIFE: European LIFE Project, led by ITC Castellón, for reducing the toxicity of Respirable Crystalline Silica.
- HIBRIMOD: Development of hybrid models, polystyrene resin and fiberglass for casting of medium-short series for the sector of machine tools. GAITEK 2015
- Creating a new integrable automatic suction molding boxes capable of extracting harmful emissions and avoid inhalation by the operator.
- PORFUND: New product development of high performance cast aluminummolds, led by Tecnalia in collaboration with Lebario
- FENOD: Improving the characteristics of the nodular iron HAZITEK change the title GAITEK 2017 and 2016
- inNew: Improved filling systems for reducing SCR environment.
- Cabin air filter - Design and development of a new air shower for removing and absorbing dust particles.
- Cleanroom; Improving the application process refractory painting by generating a white room or without external contamination. 2i funded by the Plan for the Promotion of Innovation and Advanced Investment - Plan 2i Innovation and Investment Advanced in 2018 and 2019
- ERAIMAT: (Project No. ZL-2020/00548) Foundries Fumbarri Durango, S.A. participates in the research project focused on developing building materials valorizing waste foundry sands. This project aims to demonstrate the validity of the reuse of this waste in concrete construction applications such as mortars, non-structural concrete or fillers, supported by the Department of economic development, sustainability and the environment, through the HAZITEK program in 2020.
- MachEASY; (Project No. ZL-2021/00176) which is being developed by FUMBARRI supported by the Department of economic development, and environmental sustainability through the HAZITEK program in 2021
- INORGANI: Development and validation of new technology for the manufacture of inorganic foundry cores and moulds. This project aims to develop and demonstrate the application of an innovative inorganic resin for the manufacture of iron foundry cores and moulds, as a substitute for organic resins. To position the Basque foundry sector as a reference in the development of advanced, clean and harmless technologies and manufacturing processes for the environment and workers' health. To combat the problems associated with polluting and harmful emissions generated by organic resins (BTX, VOCs, ...), and to improve the recyclability of waste sand.